Innovation in the textile industry has bringing new materials to the forefront that have been found to be playing increasingly important roles in modern day daily lives. Textile films is an example of an innovative product that has swiftly become an essential component of textiles used in the hygiene and medical industries. Textile films are primarily made of polymers or other advanced composites with mechanical properties such as strength and flexibility, as well as surface properties such as hydrophoby or oleophoby, that help them meet the demands of various industries such as packaging, medical, and technical clothing.
Multibeam extrusion technology is used to make textile film. Nonwoven films are made by assembling tiny fibres into a sheet or web and joining them either mechanically with an adhesive or thermally by applying a binder and melting it onto the web as the temperature rises.
The nonwoven industry is one of the fastest growing across all industries, and the textile film market has a significant share of it. Textile films market size was USD 5,190.2 million in 2020, according to Reports and Data, with a projected CAGR of 6.30 percent. They’re utilised in everything from clothing to baby wipes. These fabrics can be single-use or limited-life, or they can be quite durable.
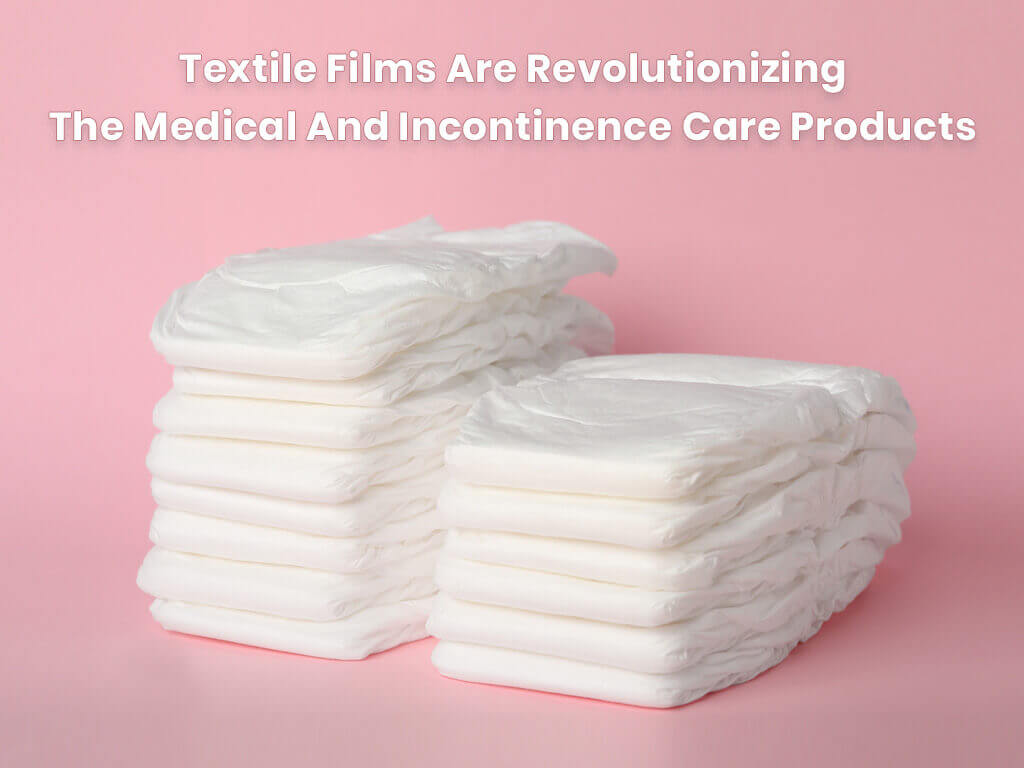
Textile films have a wide range of uses in the medical and healthcare industries. Nonwoven textile films have particular advantages over more typical fabric formation methods since they may be made directly from fibres at a reduced cost. As a result, the nonwoven approach is well suited to the creation of disposable items, which help to maintain the high standards of hygiene required in medical settings by reducing the risk of cross infection. For items that require liquid barrier protection, absorbency, filtering efficiency, softness, and other characteristics, a wide range of disposable nonwoven products are now available.
The use of disposable products has increased due to a substantial increase in the use of reusable linen items as a result of rising labour costs and a higher awareness of hygienic issues. Adhesive bonded textile film materials, such as nappy liners and entire throwaway products, are commonly utilised in hospitals and sanitary applications. Disposables are established in these domains on the basis of practicality and hygiene. Softness, opacity, substance, surface texture, absorbency, low static, comfort, acoustic deadness, porosity and enhanced liquid holding capacity, as well as fast drainage, are all advantages of developing low bulk density non-woven fabrics for surgical-care products.
Advantages of Textile Films:
- Absorbency
- Resilience
- Liquid Resistance
- Stretch
- Softness
- Strength
- Flame resistance
- Washability
- Cushioning
- Filtering
- Sterility and Bacterial Barriers
Textile Films In Medical Products:
Textile films are utilised in a variety of applications, although they are most typically used in medical and hygienic settings. Medical textiles items are divided in three groups namely patient-specific, general patient management, and procedure-specific. Sponge, linens, burn sheets, and other patient-specific products are included in medical textiles. Patient management goods include underpads, adult diapers, and wipes. Sterilization wrap, surgical gowns, drapes, table covers, face masks, and head and shoe covers are among the third category of procedure-specific items.
Textiles used in operating and emergency rooms include surgical gowns, patient drapes, caps, masks, and cover cloths of all sizes. Protective medical textiles are designed to keep healthcare workers safe from blood and other infectious fluids. The Occupational Safety and Health Administration (OSHA) defines biological protective clothing as clothes that under normal conditions of use and for the duration of time of use, will prevent blood and other infectious materials from reaching user’s work clothes, street clothes, undergarments, skin, eyes, mouth, or other mucous membranes.
A protective textile garment must meet two essential characteristics, according to this definition: it must prevent infectious elements from flowing through the skin and it must endure long enough. In the medical industry, protective clothing has to be inexpensive, breathable, comfortable, durable, and effective. Hospital now use clothing that are made with coating and laminating technologies that lead to the development of lighter, more comfortable, and more protective garments for operating room staff and patients are being used.
The coronavirus pandemic and the ensuing emergency that the whole medical community faced has helped in bringing greater attention to medical clothing. At various points in the crisis, a personal protective gown has been the only barrier between a caregiver and a patient infected with the deadly coronavirus infection. PPE has been so invaluable and in such short supply during the peak of the crisis that medical practitioners have gone without break and even even and water for quite long durations just to make sure that PPE kits are used to their fullest extent. Therefore these PPE kits deserve the best materials and technologies and the recent pandemic has made sure that greater investment is being made in improving medical textiles.
Textile Films That Act As A Barrier:
It is critical that the operating room environment be kept clean and that infection control be strictly enforced. The pollutant particles shed by the nursing personnel, which include bacteria, could be a source of illness for the patient. Surgical gowns should thus act as a barrier to prevent polluting particles from being released into the air. Barrier requirements might range from particles and germs to fluids and viruses, and can be partial (resistant) or total (proof). Fabrics reinforced with impermeable film are currently the only items that regularly pass the viral barrier test.
The requirement for medical professionals to wear clothes that provide a barrier to fluids such as water, blood, and alcohol has become crucial with the rapid development in blood borne diseases such as hepatitis C and HIV. Simple slip-on body covers and instrument wraps to elaborate 3-D structures like masks are examples of these things. The main requirements for barrier fabrics are that they resist liquid penetration, notably blood, while still being hygienic, breathable, flexible, and affordable. Because of these requirements, the majority of barrier garments are constructed of non-woven materials or textile films, which are very affordable and may be discarded after each use, decreasing the need for re-sterilization. Special breathable films are sometimes applied to fibres and fabrics. In certain circumstances, chemicals are directly added to the polymers that are used to produce the fibres.
Textile Films in Incontinence Care Products:
The term incontinence refers to an unintentional loss of bladder and bowel control. Incontinence is a common problem. Mattress protectors are one type of product that can help with such issues. The soft polyester top and bottom absorb all moisture, while the vinyl centre keeps liquids out. Dignity pants are composed of polyester and cotton with a large dry-guard barrier panel for secure leak prevention and bowel protection.
By introducing a diaper that could absorb 10 times its weight, textile films material revolutionised the diaper industry. This is due to the diaper’s composition of polymers, nonwoven fabric, and wood pulp. Tampons and sanitary napkins, panty liners, incontinence products, nursing pads, and toddler training trousers are some of the other typical uses.