Cruise ships, LNG carriers, container ships, and special ships for transporting automobiles all use marine plate heat exchangers. Some of these rules also apply to high-end tourist cruise ships. The application has a lot of features, so that’s a plus.
For marine plate heat exchangers, the most common applications include cooling the lubricating oil used in the ship’s main engine (the lubricating oil cooler), cooling the ship’s main generator, and cooling the main engine and auxiliary machinery (the central Coolers); and seawater desalination.
Marine Plate heat exchangers exporters for ships have several distinct advantages, the most obvious of which is the corrugated plate’s high performance and heat transfer efficiency. They are also small, compact, and take up no room, and they start quickly regardless of the time or environment. They are also simple to maintain and disassemble, whether for cleaning or replacing plate gaskets.
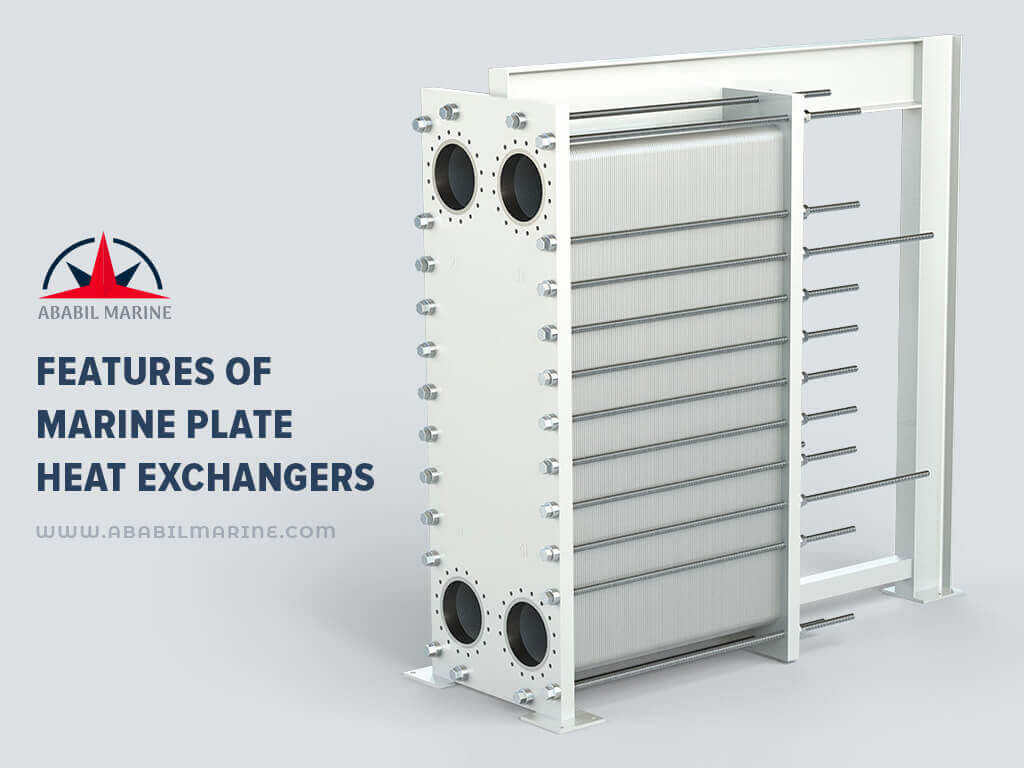
Features of Marine plate heat exchangers
The compactness and construction of naval equipment are small.
Marine Plate heat exchangers suppliers for marine turbines are currently much smaller than conventional heat exchangers, according to current thinking. Unnecessary board parts should be removed or reduced based on the actual stress and strain distribution, and weak areas should be locally thickened in order to meet marine equipment requirements.
When welding, the inner plate and panel are welded together to eliminate any remaining stress, and then the gas cutting method is used to reduce the impact of welding deformation on overall body strength. It will be able to make the most of the equipment in a small area, which will result in greater savings. It will also finish the heat transfer work to ensure that the ocean can be used normally in the future.
There must be an impact, big angle vibration, and other qualities in marine equipment for it to be used.
The bottom of the plate has a multi-point fixing method, which means a fixed connection can be used for all fixed parts. The “ribbed” structure of some critical special parts also greatly improves the equipment’s stability. The heat exchanger’s efficiency and effect can only be ensured if the installation is more stable. When this happens as a result of issues such as vibration, it has an impact on the heat transfer.
Cooling should take into account that seawater contains large levels of both hydrogen and nitrogen ions.
Since many seawater-based turbines are in operation, they have a significant impact on the heat transfer medium. As a result, today’s turbine sheets are typically made of a material with high corrosion resistance, such as titanium, which has a much lower quality than stainless steel. Additionally, to routine inspection, the titanium plate underwent a 100 percent color penetration test to eliminate any errors in plate sampling. This helped to ensure the quality of the titanium marine Plate heat exchangers.
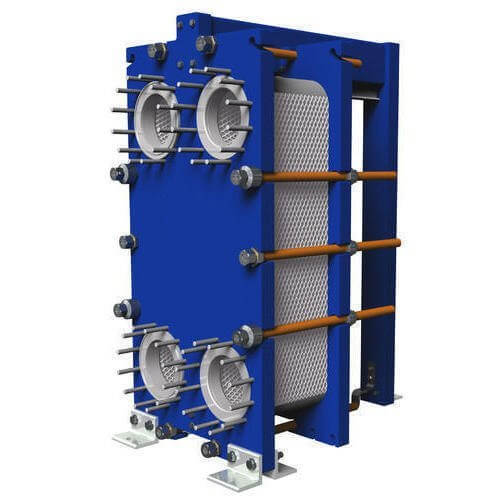
Heat transfer medium
Because the specific heat capacity difference between water and oil is so large, the temperature difference and heat transfer coefficient are also very large during heat transfer. Oil-water heat transfer performance must be ensured under ship working conditions in order to ensure that the equipment has a certain heat exchange margin in order to make the product reliable and cost-effective. Only when the heat medium is capable of efficiently conducting heat can the heat transfer effect be obtained.
Plate-type heat exchangers (PHEs) are designed to allow fluids to transfer across a larger surface area. Marine Plate heat exchangers have a high thermal efficiency because heated fluid flows downward and cold fluid flows upward over huge exposed plates. Cross-flow and the corrugations in the plates increase turbulence and lower the Reynolds number in a PHE compared to a standard tube type heat exchanger (Re).
The joint material used in marine plate heat exchangers is often ‘nitrile rubber,’ which is adhered to the plate using an adhesive like ‘Plibond.’ Asbestos fiber compressed in a joint material form is another option for high-temperature joints (CAF). The nitrile rubber can withstand temperatures up to roughly 100 degrees Celsius without cracking or melting. As the temperature rises, the rubber hardens and loses some of its pliability. When the cooler is put together and the clamping bolts are tightened, the rubber joints become compressed.
Chevron corrugated marine Plate heat exchangers can be damaged if they are overtightened. Overtightening causes the cooler’s pressure drop to increase as well. Similarly, plates that are too slack lead to a poor seal between the plates themselves.. Plate cooler dimensions are examined as it is tightened and loosened. To avoid leaks, clamps should be used on all joints.
All liquid inlets and outputs have a permanent endplate. The moveable ends are supported by the horizontal carrying bars, where the plates are likewise positioned and supported. The flow apertures on the corners of the plates are positioned so that the cooling liquid and the cooling liquid alternately pass between pairs of marine Plate heat exchangers. When liquids are travelling in opposite directions, the efficiency is maximized. Except for the double joint at the ports on one side of the plate, joint leakage is clearly evident from the outside. A drain hole serves as a marker for his particular portion.