Types of plate heat exchanger on a Ship
Onboard a ship, various types of plate heat exchanger are used. The type of heat exchanger used for a specific application is determined by the application and requirement. Almost every system on a ship is dependent on a heat exchanger, which either cools or heats the fluid.
The following are the exchanger types, which are primarily defined by their construction:
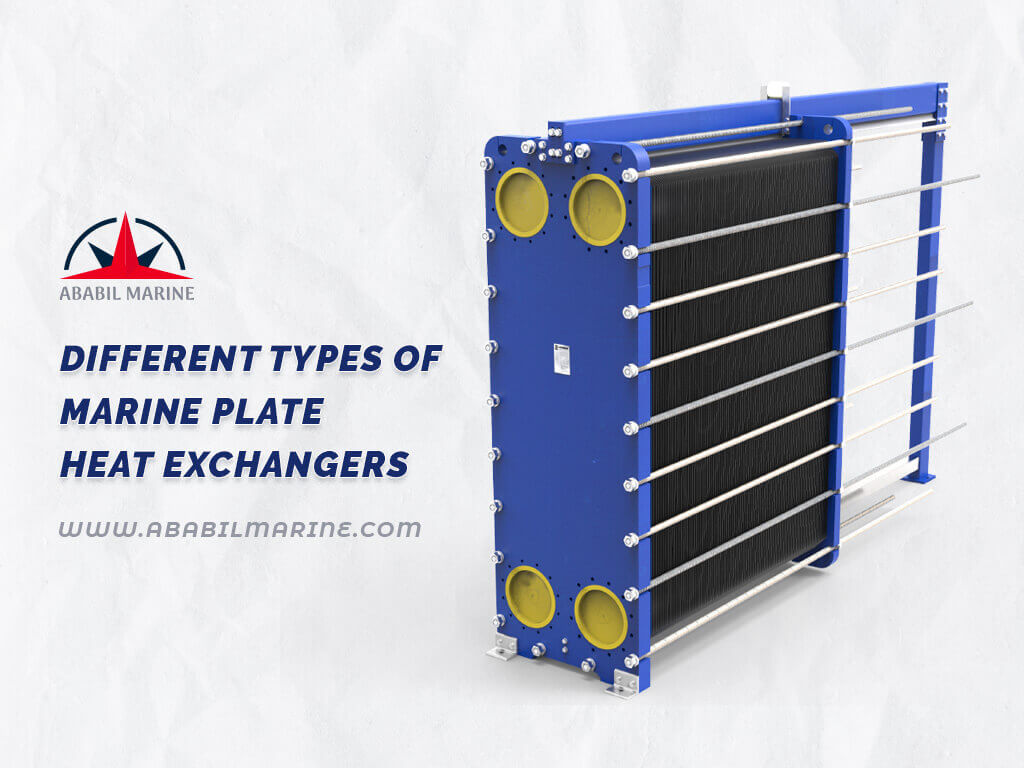
1) Shell and Tube Type plate heat exchanger
This is the most common type of design, with a shell surrounded by several tubes, and the flow of liquid to be cooled is primarily through tubes, while the secondary liquid flows over the tube inside the shell.
The shell and tube plate heat exchanger exporters is extremely cheap to install and clean, but it requires more maintenance than other designs.
The entire shell of this plate heat exchanger is fitted with a tube stack, also known as the shell. Two end plates are sealed on both sides of the shell, and a provision is made at one end to accommodate expansion. The cooling liquid flows into the tube plate through tubes that are sealed on either end. Bell mouthing and expansion secure the tubes in the tube plate.
The shell is completely surrounded by water chambers that surround the tube plates. Coolers could be single pass or double pass, displaying the flow of cooling liquid.
To prevent leaks from the cooler, gaskets are installed between the tube plates and the shell, as well as between the tube plate and the end cover.
The unfixed side of the tube plate is free to move and has seals on either side of a safety expansion ring. The cooling liquid or liquid to be cooled may then leak out and become visible, preventing intermixing or contamination.
Traditionally, the main engine cooling freshwater cooler and the main engine lube oil cooler have been circulated with seawater, which appears to pass through the cooler’s tubes.
The shell, on the other hand, comes into contact with the liquid being cooled, which is typically lubricating oil or distilled freshwater laced with corrosion-inhibiting chemicals that are added directly to the expansion tanks to maintain a thin protective layer inside the pipelines and thus prevent corrosion. Drew Marine offers Liquidewt, and Unitor offers Rocor NB liquid, both of which are commonly used for corrosion inhibition. The shell could be made of steel or cast iron. The coolers should be installed vertically to ensure automatic air venting from the system, as the airlock causes excessive overheating and reduces the effective cooling surface area of the liquid being cooled.
Baffles are installed on the tube bundle, allowing the liquid to be cooled up and down, increasing the effective surface area of cooling. They also provide strength and rigidity to the bundle by supporting the tubes.
2) Plate Type Heat Exchanger
Plate exchangers are made up of thin corrugated plates that are joined parallel to form a cavity for fluid flow inside. Heat transfer occurs between two different fluids on opposite sides of the plate.
This type of plate heat exchanger suppliers is more expensive to install than shell and tube heat exchangers, but it has a much lower maintenance cost.
For the same size unit, the efficiency of the plate type is higher than that of the shell and tube types, and it can withstand high pressure.
Plate type coolers can be easily opened for cleaning and are thus easy to install and clean due to the small amount of space required for their installation.
They outperform shell and tube coolers of the same size and capacity. They are made of similar metal plates with patterned corrugation that are joined together by nitrile rubber joints.
3) Plate Fin Heat Exchanger
A plate and fin heat exchanger is similar to a plate-type exchanger, but it also has fins to increase system efficiency. Aluminium alloy is used because it improves heat transfer efficiency and reduces unit weight.
Offset fins are fins that are fixed perpendicular to the direction of flow. Straight fins are those that are fixed parallel to the flow direction. Wavy fins are fins that have been fixed in a curvature form to increase the heat exchanging effect. The efficiency of this plate heat exchanger is slightly higher than that of a plate type device, but the installation and maintenance expenses are higher.
4) Dynamic Scrapped Surface Heat Exchanger
Because of the continuous scraping of the surface, this plate heat exchanger has a long running time, which aids in heat transfer efficiency and reduces system fouling.
The scraping is done by a blade unit that is powered by a motor-driven shaft and a timer that moves inside the frame. This heat exchanger is typically used to increase the turbulence of a highly viscous fluid in order to transfer heat. Because of the auto cleaning process, maintenance costs are lower when compared to other types.
5) Phase Change Heat Exchanger
This type of plate heat exchanger, as the name implies, is used to change the phase of a medium from solid to liquid or liquid to gas using the principle of heat transfer. This type is normally operated in freeze and melt cycles to allow for phase change.
The plate heat exchanger is typically built like a shell and tube exchanger, but with at least two divider walls to create upper and lower annular spaces for flow passage. It also has fins in both passageways to aid in heat transfer.
6) Spiral Heat Exchanger
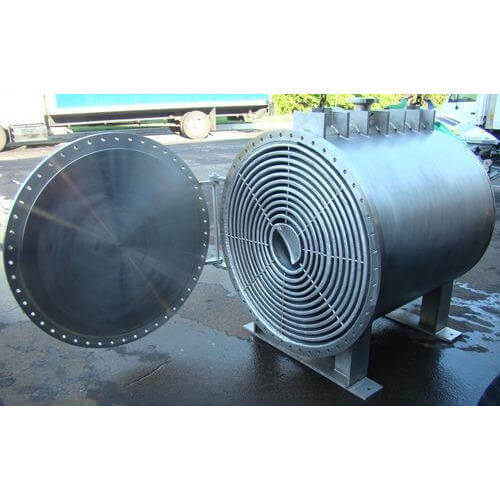
This sort of heat exchanger is made up of concentric form flow channels that help to create a turbulence flow of a fluid, enhancing heat transfer efficiency. The initial installation cost is higher, but it is much more efficient than other types because of the compact size. When compared to other types of units of the same size, the maintenance cost is the lowest.
A spiral’s fluid flow is rotating current flow, which has the property of self-cleaning of fouling within the spiral body.
7) Direct Contact Heat Exchanger
There is no dividing wall within this sort of new and refurbished plate heat exchanger. For the heat transfer process, both media are in direct contact. Direct contact heat exchangers are further characterised as follows:
1. Gas-liquid
2. Immiscible liquid-liquid
3. Solid-liquid or solid-gas