A plate heat exchangers are a product of over 35 years of experience in the marine engine industry. Having been in the heat exchanger industry for such a long time, WCR has more cross-brand knowledge than any other company in the industry today. A vast amount of information has been collected as well as the top Application Engineers have been recruited. In terms of performance, maintenance, and economy, we now offer competitive heat exchanger solutions.
What is a Plate Heat Exchanger?
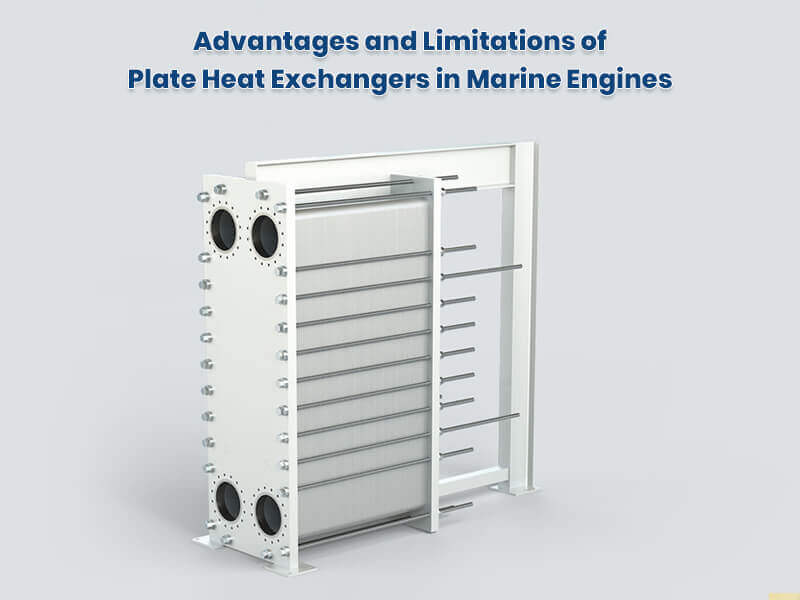
Because of its low cost, flexibility, ease of maintenance, and high thermal transfer, the plate type heat exchanger is the most efficient type of heat exchanger available. Heat transfer is accelerated by creating turbulence in the entire heat transfer area by using WCR plate corrugations. Heat transfer coefficients are maximized, and pressure drop is minimised, allowing for close temperature approaches. As a result, heat transfer surfaces are smaller, units are smaller, and heat exchangers are fewer. Customers benefit from less space reduced secondary flow rates, and smaller pumps as a result of this.
In the WCR Plate Heat Exchanger, a particular number of gasketed plates are fastened between a top carrying bar and a bottom guide bar. Ties bar between stationary frame plate (the head) and moveable frame compress the plates (the follower). By means of frame connections, fluids are introduced into the marine plate heat exchanger and distributed between its plates. Gaskets are used to control the flow through the alternate passages between the plates. Depending on the application, these are available in single-pass and multi-pass configurations.
Advantages of Plate Heat Exchanger in Marine Engines
Here are the top 7 advantages of plate heat exchangers below :
Easy to Remove and Clean
Simple, just unscrew the tie bolts and slide the movable frame back into place! As a result, the plate pack is ready to be examined, pressure cleaned, or even removed for refurbishment.
Expandable
The plate heat exchangers has the advantage of being expandable, which allows for an increase in heat transfer capability. Heat transfer requirements can be adjusted by simply adding plates instead of purchasing a new frame unit, saving both money and effort in the long run in marine engine parts.
High Efficiency
Although fluid velocity is relatively low, high turbulence is possible due to the plate patterns and narrow gaps. When combined with a counter-directional flow, this results in very high heat transfer rates.
Compact Dimensions In order to achieve the same heat transfer efficiency, a much smaller heat exchanger is required due to the high efficiency. Plate heat exchangers typically takes up 20-40% less space than a shell and tube heat exchanger does.
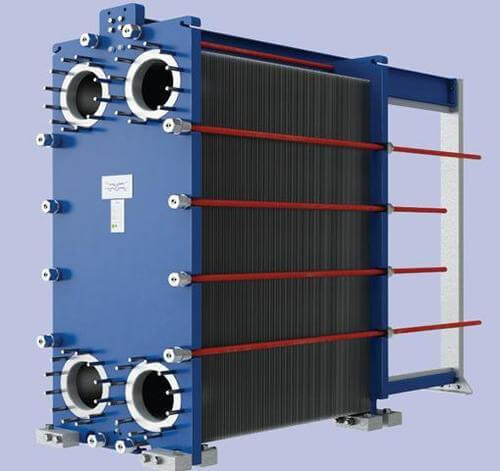
Close Approach Temperature
Plate heat exchangers high efficiency is due to the same features that allow them to reach close approach temperatures, which is critical in heat recovery and regeneration. Near-freezing temperatures are possible.
Multiple Duties in a Single Unit
Simple divider plates or more complex divider frames with additional connections can be used to separate the new and refurbished marine plate heat exchangers into sections. Heat, regenerate, and cool a fluid can be done in one heat exchanger, or multiple fluids can be cooled and/or heated using one cooling or heating source.
Avoid cross contamination
Gaskets are used to seal each medium, preventing cross-contamination.
Less Fouling
The pattern of the plates, the many contact points, and the narrow gap between the plates all contribute to a very high level of turbulence. Fouling is significantly reduced compared to other types of heat exchangers because of this, along with the smooth plate surface.
Lower Costs
High heat transfer coefficients result in smaller heat exchangers and smaller heat transfer areas, and in some cases, even fewer heat exchangers altogether. This, as well as reduced space requirements, reduced flow rates, and smaller pumps, translates into a more efficient system.
Limitations of Plate Heat exchangers in Marine Engines
- The initial cost is high due to the high cost of titanium plates.
- Since tube coolers are more difficult to test for leaks, finding leaks is more difficult.
- The cooler’s operating temperature is limited by the bonding material between plates.
- Compared to tube cooler, plate cooler has a higher pressure drop.
- A lot of disassembly and reassembling to do
- As a result of overtightening the clamping bolts, pressure drops across the cooler increase.
- It is possible for joints to degenerate depending on the operating conditions
- Other parts of the cooling system are susceptible to corrosion because Titanium is a noble metal
heat exchanger transfers or “exchanges” heat to enemies pumped by water outside the boat for the ship’s engine cooling water. Raw water pumped through a small bundle of tubes in a chamber filled with hot engine cooling water.. Ababil marine is the leading Plate Heat Exchangers Suppliers providing the best deals. Search the best plate heat exchanger manufacturer – Ababil marine.