Hydraulic Pumps of various sorts, such as centrifugal pumps, axial flow pumps, plunger pumps, and mixed pumps, are used aboard ships for a variety of applications.
Marine pumps can be used for cooling, fuel oil transfer, lube oil transfer, F.O. and F.S. cargo pumping, cargo stripping, hydrophore tank unit, freshwater generator, oil-water separator, incinerator, sewage treatment unit, ballast, circulating, general service (G/S) fire fighting, boiler feed water, condensate water, fresh(drinking) water, sanitary water, Sludge and bilge, and other applications.
Marine Hydraulic supplier are a large subject in and of itself; in this piece, I’ve discussed all of the pumps that fall under the generic pump categorization.
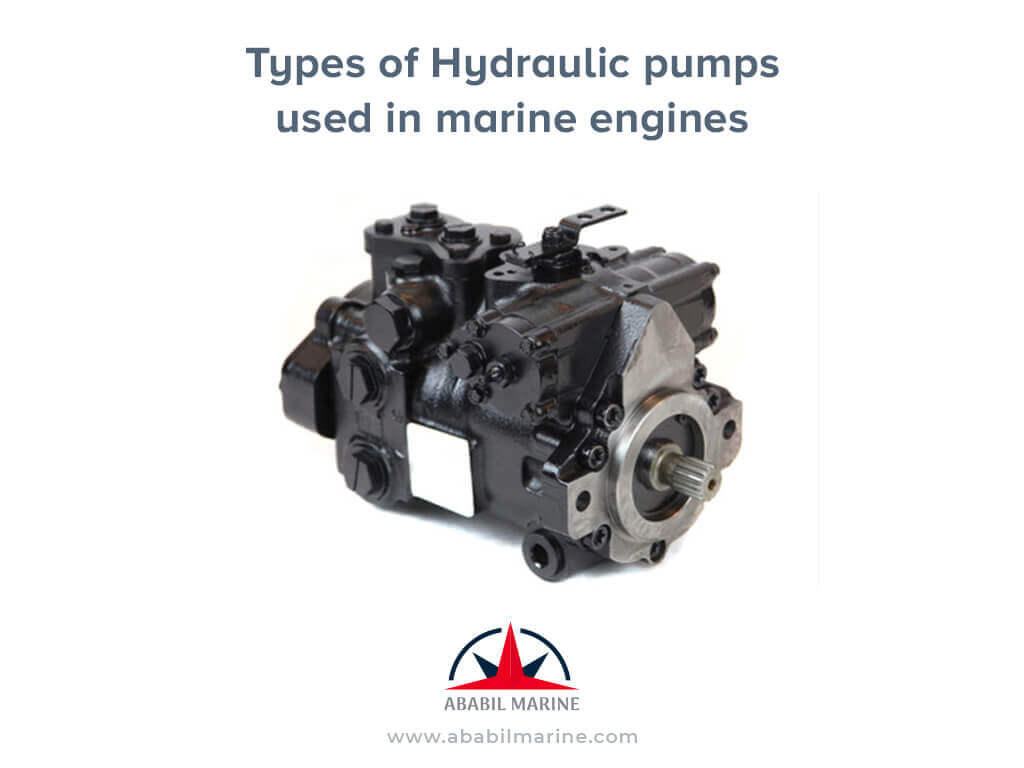
The pump is a mechanism that transforms mechanical energy into potential energy, kinetic energy, thermal energy, and pressure energy of the fluid, and it is used to elevate liquid from a low to a high level. The pump is a device that transports liquids.
Different Types of Hydraulic Pumps
Best Supplier Of New And Re-Furbished Marine Hydraulics Pumps are typically divided into two types: positive displacement pumps and dynamic pressure pumps (Roto-dynamic pump).
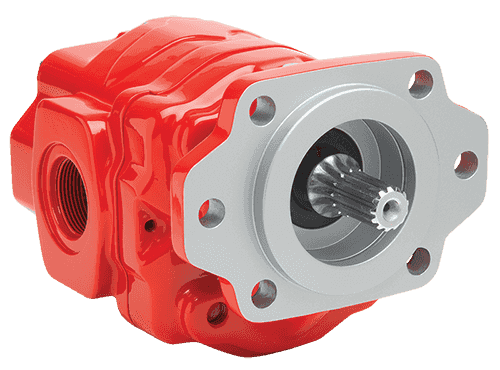
Double acting piston pump
1. Positive Displacement Pumps
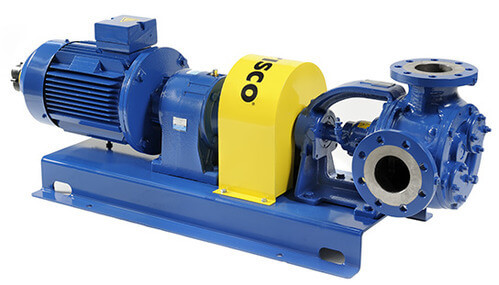
Positive displacement pumps are described as hydraulic pumps that generate suction by expanding the volume of the chamber in which fluid is trapped by mechanical variation on the suction side and discharge by mechanically decreasing the volume of the chamber in which fluid is trapped.
Positive displacement implies that once the fluid is caught in the chamber by suction and has no way to return to suction or churn, it must be released, which means that a Positive displacement pump must be operated with its discharge valve open at all times.
If a positive displacement pump operates against a closed discharge valve, the pressure will rise dramatically until there is a rupture in the pump pipe or the pump itself is badly damaged – or both.
To avoid such an accident, a relief or safety valve, either internal or exterior, must be installed at the discharge line. As a precaution, an internal safety valve is supplied, while the exterior relief valve provides feedback to the suction line.
1.1 Reciprocating pumps :
The phrase “reciprocating pump” refers to hydraulic pumps that move fluid from the suction line to the discharge line in a back and forth motion. Water or other liquids are moved by a plunger or piston that moves back and forth inside a cylinder in a reciprocating pump.
It is found under Reciprocating pumps. Pumps (a)Piston Pumps (b)Plunger Pumps (c)Bucket pumps.
Piston pump:
This pump is made up of a piston that travels back and forth to pump fluid from low to high levels. It is further classified into two types: single acting and double acting.
Single Acting Piston Pump
This pump is frequently used as a bilge pump or tank stripping pump. The design is straightforward, strong, and dependable. Materials vary depending on the use, although bronze is commonly used for bigger components and stainless steel for piston rods.
Plunger pump:
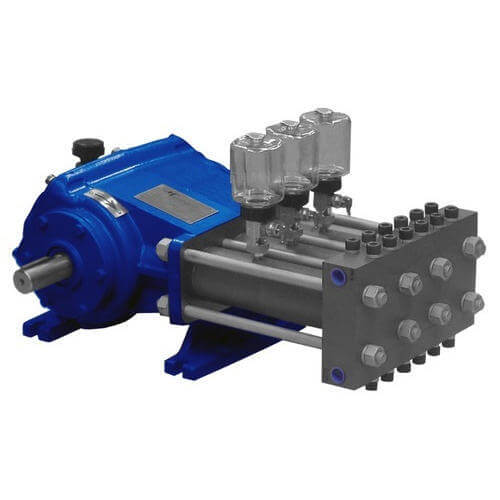
This pump is made up of a plunger (Cylinder) that travels back and forth to pump fluid. The only difference between this pump and a piston pump is that the plunger replaces the piston. A smooth cylinder slide and a high-pressure seal keep the pump from leaking.
Bucket Pump:
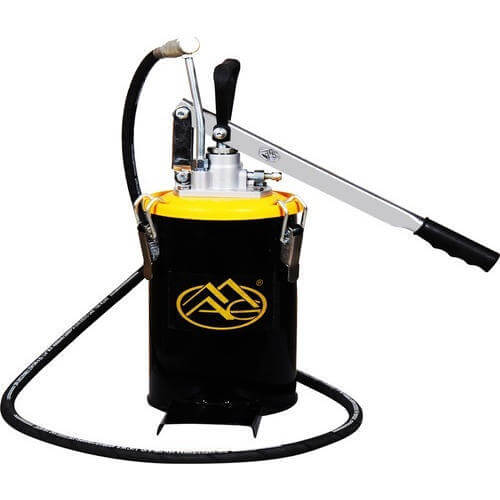
A simple bucket pump is similar to a lift-Disc pump, except it does not need the use of a pipe to pull the liquid. Traditional bucket hydraulic pumps are utilised in a rural community when there is no electricity and the ground has a low water capacity.
Bucket hydraulic pumps were formerly utilised in ancient turbine ships and are currently employed as a high-pressure complicated bucket pump for lubricating. On a ship, a contemporary bucket pump is used to inject or spread a predetermined volume of Greece or lubricating oil while the plunger of the pump is worked.
1.2 Semi-Rotary Pump:
These hydraulic pumps, as the name implies, are used on tiny offshore vessels to pump a little amount of fluid. They only move in an arc and do not fully spin.
Semi-Rotary (Hand) Pump
Application
- It is used for bilge pumping.
- Adding diesel oil, lubrication oil, and lube oil to the crankcase of a diesel engine
- To dispense gasoline, biodiesel, and ethanol mixes.
- This pump can handle water, lubricating oil, and diesel oil. The only care you’ll take before utilising it for various fluids is to properly clean the pump to ensure there’s no contamination.
- These pumps are not intended for highly thick fluids such as grease.
1.3 Rotary Pumps
Rotational pumps are those that pump fluid by rotary motion. They are not to be mistaken with centrifugal pumps since the fluid in this pump is trapped in a cavity while the pump rotates, and the only movement of fluid is forward and not backward, that is toward the suction, nor can it churn.
Rotary hydraulic pumps are further classified as (a) constant-delivery pumps and (b) variable-delivery pumps.
Constant Delivery Pump
A Consistent Delivery Pump is one that has a constant discharge rate throughout its operation..
Gear Pump
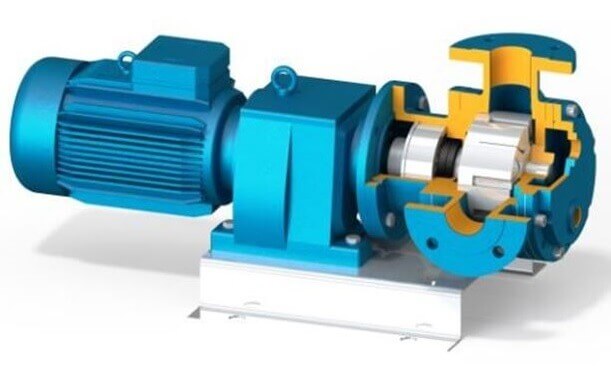
( i ) Gear Pump: Gear pumps operate on the idea of fluid being trapped in the cavity produced between the gear and the pump’s housing as it meshes in and out of gears.
The clearance between the top-land and casing is measured in thous (1/1000 inch); this tight clearance, along with the fast rotational speed, efficiently prevents fluid from flowing rearward. One gear is called driving gear, while the other is called driven gear or idealer. There are two kinds of gear pumps: exterior and internal.
( ii ) Screw Pump: Screw hydraulic pumps employ one or more screws to transfer fluid from suction to discharge. The screws revolve on their axes inside the cylinder, trapping fluid in the cavity and pushing it forward. Fuel oil transfer pump is an example of such application.
Vane Pump
( iii ) Vane Pump: The vane of a Vane Pump is flexible and may expand and retract when spinning on the shaft within a huge circular chamber; the shaft is off-center from the pump casing, resulting in eccentricity. On the intake side, the vane expands, increasing the area available for suction, while on the discharge side, the vane retracts, resulting in discharge.
Lobe Pump
( iv ) Lobe Pump: Because of its huge pumping chambers, the Lobe Pump is employed on board ships where there is a risk of solid contamination. The lobe within the pump does not come into touch with anything. Lube oil scavenging pump and lube oil circulation pump
Variable Delivery Pump
A variable delivery pump is one whose discharge changes depending on the requirement. It is utilised in situations where there must be a constant shift in fluid flow. The variable displacement pump works on the idea of changing the pump stroke to alter the amount of fluid displaced based on the need.
The variable displacement pump’s primary components are the floating ring and the swash plate. Keep in mind that these pumps always have an odd number of hydraulic pumps. Fin Stabilizer, Steering Gear are examples of applications.
( i ) Heleshaw Pump :
Heleshaw pumps are classified as variable displacement hydraulic pumps. Although the operation of the Hele shaw pump is explained in numerous books and articles in a complex manner, the fact is that it is simple.
This pump is linked to a motor, which rotates the shaft at a constant speed to which the cylinders are attached. The Floating ring is moved by mechanical linkage, and this movement causes eccentricity of the concentric Floating ring and piston.
While a result, as the pump rotates in an eccentric condition, suction and discharge occur.
The eccentricity of the floating ring determines the piston’s stroke; the floating ring also accommodates slippers. While the concentric condition is maintained, neither suction or discharge happens; however, when eccentricity develops, suction and discharge begin. The flow direction is determined by the position of the floating ring.
( ii ) VSG Pump:
VSG pumps are a more sophisticated form of variable displacement pump with an axial piston configuration that operates on the concept that “a reciprocating piston pulls in liquid during retraction and discharges liquid when it extends.”
Casing, Cylinder block, Piston, Driveshaft, Swashplate, Adjusting valve, and Inlet & Outlet ports are the essential components.
A swash plate is used to generate the reciprocating motion of the axial piston in this case. In variable displacement hydraulic pumps, a swash plate is a mechanism that converts the rotating shaft motion to the reciprocating motion of the axial piston.
VSG pumps are sometimes known as swash plate pumps due to their implications. On big ships, these hydraulic pumps are often employed as steering hydraulic pumps.
The piston, together with the piston barrel assembly, revolves around the shaft in the VSG pumps due to the swash plate design. The axial piston moves synchronously thanks to a contact between the swash plate surface and the piston shoe.
During one half of the revolution, the piston travels out, increasing the volume inside the cylinder; during the other half, the piston moves in, decreasing the volume. This continuous process causes the pump’s suction and discharge.
Advantages
There are several advantages to utilising VSG pumps in the steering system over conventional hele-shaw hydraulic pumps.
1. Its capacity may be readily adjusted by adjusting the angle of the swash plate. (The angle of the swash plate is proportional to the discharge.)
2. It is highly cost effective and requires little upkeep.
3. It can operate at a higher speed than traditional hele-shaw pumps.
4. It is simple to use thanks to constant speed motors.
5. It is ideal for 4-Ram configurations.
2. Roto-Dynamic Pump
A Dynamic Pressure Pump (Roto-Dynamic Pump) is a pump that continually adds energy to the fluid within the pump. This causes a rise in fluid velocity, which may later be decreased to raise pressure.
This pump may require priming, in which case a reciprocating pump may be used.
2.1 Centrifugal Pump
A centrifugal pump is a mechanism that employs spin to impart velocity to a liquid, which is subsequently converted into flow. This definition reveals two facts about centrifugal hydraulic pumps.
(1) The impeller imparts energy to the liquid in the form of velocity.
(2) The casing of the centrifugal pump converts energy into flow. This pump consists of an impeller and a casing that work together to provide a constant pressurised flow. Application: Firefighting main pump for general service, nozzle cleaning, hydrophore supply.
A. Volute Casing Centrifugal Pump
Volute Casing Centrifugal Pump is a centrifugal pump casing in which the cross-section of the casing gradually rises as the fluid travels toward discharge.
This increase in cross-section causes a drop in fluid velocity, which results in a decrease in kinetic energy, which is converted into pressure energy. In a volute centrifugal pump, the shaft is eccentric.
Vortex Casing
B. Vortex casing Centrifugal Pump
In this pump, there is a circular chamber between the impeller and the casing, and the liquid first enters this circular chamber (Vortex) before entering the volute casing. By using vortex casing, eddy loss is significantly reduced, and the efficiency of conversion from K.E. to pressure energy is increased when compared to volute casing.
2.2 Axial Pump
Axial pumps are those in which a propeller is employed to increase pressure by imparting axial acceleration to the fluid to be pumped. This pump has the greatest flow rate of any pump. When idle, these axial flow hydraulic pumps produce relatively minimal flow resistance. Fin stabiliser and bow thruster are examples of applications.
Ababil marine provides high quality Hydraulic pumps from leading brands like REXROTH and HAGGLUNDS.